
Special designs
Special challenges require special solutions.
Every task or challenge has its own particular requirements and needs to be addressed. While a one-size-fits-all solution can be simplistic in some cases, it is often more effective to develop individual solutions tailored to the specific requirements. Whether the goal is to increase efficiency, reduce costs or improve safety, customized solutions can help companies achieve their goals.
Planning
Share your targets with us! We are happy to provide you with advice and trend-setting support and develop specific manufacturing solutions for you in order to realize your ideas and concepts.
Engineering
With our experienced team of engineers and designers, we develop and produce individually, customized and optimally tailored to your requirements. From the drawing to the 3D model.
Implementation
We take over the entire project management for you and help you with the montage and acceptance of your components. And even after commissioning, we are there for you with our support.
Behind every challenge is the opportunity for innovation
Process flows and industries are continuously subject to dynamic development. The energy transition and climate change will still cause many changes, but also unleash potentials. Schütte Industrieservice and its interdisciplinary team have been able to co-develop and optimize innovative technologies in many industrial sectors. We develop profitable and resource-saving solutions for and with our customers and focus on optimal project execution.
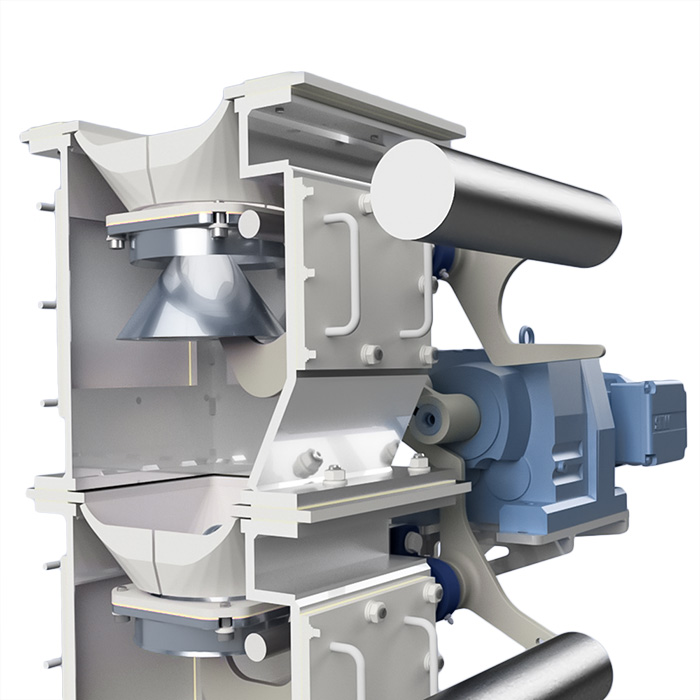
Segment valve
The segment valve is a special design of a gate valve and offers a closing process especially optimized for abrasive bulk materials. Abrasion and wear on the material can thus be reduced.

Function
Gate valve with asymmetrically rotating blade for the separation of material flows. Hydraulic drive on both sides for short closing and opening times.
Material, gas and pressure tight to the atmosphere.
Application area
E. g. as an emergency shut-off, silo closure or process valve. Also suitable for difficult, highly abrasive bulk materials, such as ceramic balls. Can be used in the high-temperature range up to 1000 °C with appropriate material selection.
- Food industry
- Feed industry
- Pharma industry
- Plastics industry
- Building materials industry
- CHP plants
- Waste incineration plants
- Process technology and plant construction
- Plants with ceramic heat carriers
Advantages
- Reduction of abrasion and wear
- Cutting flowing columns of material
- Suitable for abrasive media
Options
- Explosion protection of actuator, solenoid valve, limit switch and junction box
Double cone valve
The double cone valve is a structural adaptation of the double flap valve and is used for reliable shut-off of difficult bulk materials in differential pressures.
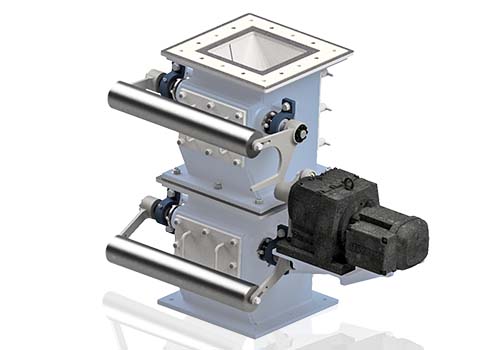
Function
Instead of the usual flap gates, two alternately opening cones are fitted in the housing of the double cone flap. Highly abrasive media can thus not affect the closing process. The fully enclosed housing is dust and gas tight to the atmosphere. The drive is electro-motoric.
Application area
This design was developed for dust discharge from the centrifugal cyclone of a sintering plant, an environment with a high dust load. The medium is highly abrasive sintered ash.
Advantages
- Simple operation monitoring without removing the damper
- Easy replacement of spare parts in installed condition
- Cone and seat particularly wear-resistant due to NiHard
Options
- Explosion protection of actuator, solenoid valve, limit switch and junction box
- Non-stick coatings/ sand bunker coating
- ATEX certificates on request
Mechanics & Function
Taking into consideration the technical requirements, we design functionality and mechanics to match your process flow and ideal economic utilization.
Resistance
We offer highly resistant materials and coatings to ensure a long and safe life of your equipment.
Compressive strength
Our special components allow safe use and tightness in high pressure areas or rooms with pressure differences.
Temperature range
All materials can be selected so that even extreme temperature ranges of up to 1000 °C can be achieved.
Sealing
We carry sealings in various materials and degrees of density. The special technology of the PAM seal developed in our company closes the passage gas-tight.
Surface finish
Depending on the properties of the medium, there are special requirements for the components. Different surface techniques can be used to optimize, for example, mechanical protection against wear or friction; barrier functions, such as corrosion resistance or thermal insulation; or interfacial interactions.
Usually our applied technologies focus on coating and finishing the surfaces. Electrolytic hard chrome plating, sand bunker painting and industrial or mirror polishing are often used.
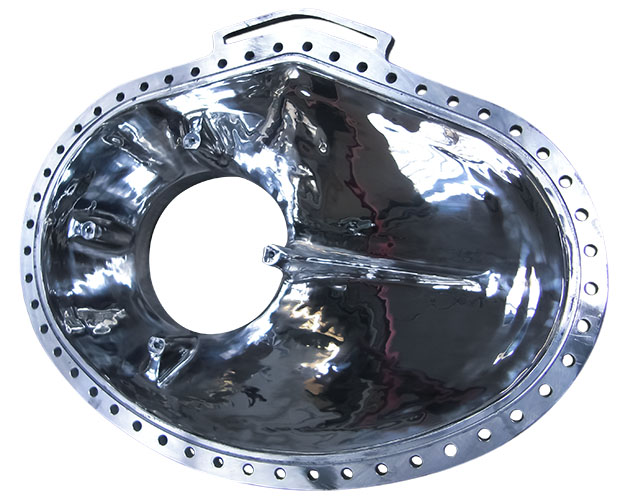
Hard chrome plating
Hard chrome-plated surfaces mainly improve the functionality of mechanically stressed surfaces. In contrast to decorative bright chrome plating, the layers are thicker and are applied directly to the material without intermediate layers.
Through an electrolytic process, a hard chrome layer is deposited on the surface of a base material, such as a ferrous material, aluminum, stainless steel, copper or brass. Layer thicknesses range from 0.1 to over 1000 µm.
With this surface technology, the components become corrosion-resistant and resistant to abrasive media due to their hardness.
This provides them with optimum protection: Damage occurs to the wear layer and not to the device. Hard chrome platings that are free of chromium6 are also considered food safe.
The technical advantages of our surface technology:
- Hardness from 68-72 Rockwell or 1100 – 1200 Vickers
- Increased tool life
- Corrosion resistance
- Increased chemical resistance
- Low cohesive friction
- Anti-adhesive properties
- Excellent gloss level
Sand bunker painting
The sand bunker coating is a “solvent-free two-component polyurethane coating”. This is usually used as an internal coating for sand bunkers, sand processing and transport facilities. However, the excellent properties have already proven themselves in many other applications within bulk solids technology. Thus, this coating can also be found in our components.
The resin-based coating is applied to interior surfaces in contact with the product, where it gradually hardens.
The high anti-friction effect of the coating prevents adhesion of the medium and its bridging. The high abrasion resistance of this tough coating protects against damage caused by striking the inner wall of the component or by the following medium. It offers high corrosion protection and is resistant to aggressive components of the molding materials due to good water, chemical and solvent resistance. At the same time, it can also be used with warm sands due to its high temperature resistance.
The technical advantages of a sand bunker coating:
- Slip-enhancing effect
- Anti-adhesive properties
- Increased tool life
- Corrosion resistance
- Increased chemical resistance
- Low cohesive friction
- High temperature resistance
Industrial and mirror polishing
In addition to the aesthetic appearance, mirror polishing offers many advantages, especially for technical applications, as the surface has a very low roughness after polishing, which means that undesirable adhesion of media can be avoided or reduced.
After mechanical polishing, the surface is removed and smoothed “flat” by a polishing carrier in conjunction with polishing agents. Depending on the material and the polishing agents, different qualities and properties can be achieved.
Thus, a passive layer of adherent, transparent, highly durable oxide, only a few nanometers thick, forms on the clean surface of stainless steel, reducing corrosion rates to insignificant levels. If the layer is damaged, such as by a scratch, it has the ability to repair itself even under a wide range of environmental conditions.
The technical advantages of industrial or mirror polishing:
- Significantly longer tool life
- Corrosion resistance
- Increased chemical resistance
- Low cohesive friction
- Anti-adhesive properties
- Excellent gloss level
Vacuum sluice
The vacuum sluice with two swing gates arranged one above the other as an infeed sluice or for discharging bulk materials from pressure systems or pressure differentials.

Function
The sequentially opening pressure-tight swing gate valves KU-HP+PAM (DN300 at inlet & DN400 at outlet) create a free passage cross-section that effectively reduces wear, blocking or sticking. For cycle-by-cycle discharge from a vacuum up to 5bar into normal pressure. Singular control signal, device continues to operate fully autonomously incl.
– Pneumatic control for ventilation and exhaust of the lock chamber, seals, flushing system.
– Fittings and lock chamber with fixed steam heating system
Application area
Due to the pressure-resistant gate valves, this structure can be used simultaneously for a positive pressure lock system up to a max. Overpressure of 6 bar and a temperature up to max. 200°C, e.g. for biodiesel production, pharmaceutical or food processing.
- Food industry
- Feed industry
- Pharma industry
- Plastics industry
Advantages
- Reduction of abrasion and wear
- Cutting flowing columns of material
- Suitable for abrasive, difficult-flowing media
- For temperatures up to 200 °C
- Gas and pressure tight
Options
- Ventilation and deaeration
- Sensor technology
- Pneumatic control system
- Steam heating system
- Flushing facilities
- Revison openings
Sluices and segment valves
Depending on the design, this model can be used under high-temperature process conditions to shut off very hot material flows.
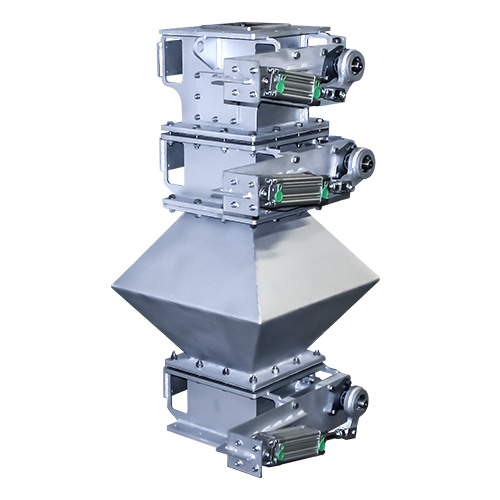
Function
This component consists of a segment valve and a double flap valve
and is designed to ensure the best possible and gas-tight isolation of the product passage even under critical process conditions, e.g. high temperatures.
Application area
The sluice and segment valve is particularly suitable for segmented feeding of free-flowing, granular bulk materials, especially at high temperatures with high hardness, e.g. ceramic heat transfer media. The unit can be mounted or installed under silos, in product lines or other bulk material handling equipment.
Advantages
- Simple operation monitoring without removing the damper
- Easy replacement of spare parts in installed condition
- Cone and seat particularly wear-resistant due to NiHard
Options
- Explosion protection of actuator, solenoid valve, limit switch and junction box
- Non-stick coatings/ sand bunker coating
- ATEX certificates on request
Pressure tight shut off valve
Pressure butterfly valve in welded construction as pressure-tight and temperature-resistant shut-off valve, ideal for changing pressure loads and extremely demanding media.
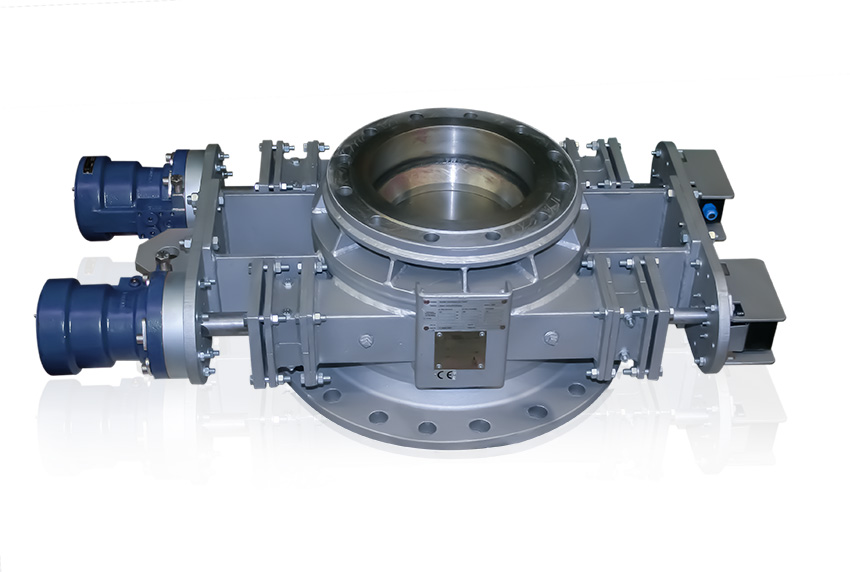
Function
The installation is made in a pipeline or to a tank. When the damper is open, the flap gate closes first and presses against the inlet seal when closed. After that, the counter lock closes. This then also presses on the lever so that a sufficiently high pressing force is built up to produce the pressure seal. With hydraulic swing drives with counter lock.
Application area
For example, in the preparation of raw silicon for the semiconductor and solar industries.
Advantages
- Pressure-tight and temperature resistant
- Suitable for abrasive media
- Changing pressure load possible (0 – 2 bar)
- Various materials and dimensions possible
Flat slide valve ZFT with flushing
Flat slide valve with position controller PMV and four water flushes in the inlet area.
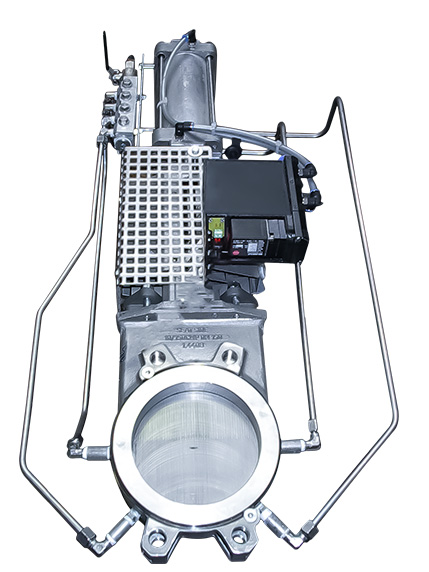
Function
Flat slide valve ZFT or also intermediate flange valve DN100 for e.g. shutting off liquid concrete. The 4 flushing connections in the inlet area have a cleaning function and prevent wear caused by contamination of the parts in contact with the process. Electropneumatic actuator connected with positioner.
Application area
- Chemical Industry
- Building materials industry
Flat slide valve VEG DN1500
shut off flat gate valve VEG DN1500 in welded construction. Compact design with side cylinders for quick emergency shut-off.
Function
Gate valve with electropneumatic actuator on both sides. Maximum temperature 400 °C, negative pressure approx. 9’000 Pa. Product or dust-tight. Can be installed vertically in horizontal piping.
Application area
E.g. as an emergency shut-off for hot winches containing clinker dust or as a filter bulkhead.
Options
- Explosion protection of actuator, solenoid valve, limit switch and junction box
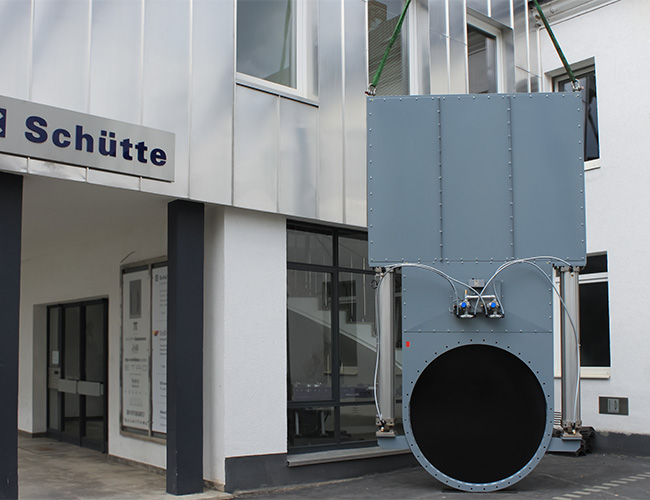